Lean Production
Essential idea: Lean production aims to eliminate waste and maximise the value of a product based on the perspective of the consumer.
Lean production considers product and process design as an ongoing activity and not a one-off task, and should be viewed as a long-term strategy.

Characteristics of lean production
Lean production aims to eliminate waste and maximize the value of a product based on the perspective of the consumer. Such characteristics include:
- Jit supplies
Getting the right amount of material to the production line JIT - Highly trained multi-skilled workforce
Having experts in place to ensure that no time is wasted - Quality control and continuous improvement
Checks are made at every stage of production to quickly identify and fix any problems that arise. Improvements to the system are actively sought. - Zero defects
Ensuring that time, material and energy are not wasted producing a sub-standard product - Zero inventory
Products are manufactured JIT to be sold
![]() |
Focuses on continual feedback and incremental improvement |

Principles of Lean Production
There are several key principles of lean production. If any of these principles are not met this could result in failure or a lack of commitment. Without commitment the process becomes ineffective.
10 principles of lean production:
- Eliminating waste
- Minimizing inventory
- Maximizing flow
- Pulling production from customer demand
- Meeting customer requirements
- Doing it right the first time
- Empowering workers
- Designing for rapid changeover
- Partnering with suppliers
- Creating a culture of continuous movement
Value Stream Mapping
Value stream mapping is a lean production management tool used to analyze current and future processes for the production of a product through to delivery to the consumer. Consider the contribution of value stream mapping to the design of an effective lean production method.

Value stream mapping allows production managers to plan the manufacture of a product from start (purchase of raw materials) to finish (sale to customer) and identify potential problems in the system.
- helps to identify Value and Waste in production
Workflow Analysis
Workflow analysis is the review of workflow processes in order to identify potential improvements. Value stream mapping provides a 'big picture' of the manufacturing processes, but workflow analysis is concerned with the details of the production line.
Identifies potential improvements by considering the sequence, tools and even worker movement to ensure the highest possible efficiency in the system.
Product Family
The concept of standardized specifications, components or assemblies within a product family or associated brands allows companies to create a competitive advantage. A product family is a group of products using similar processing methods.
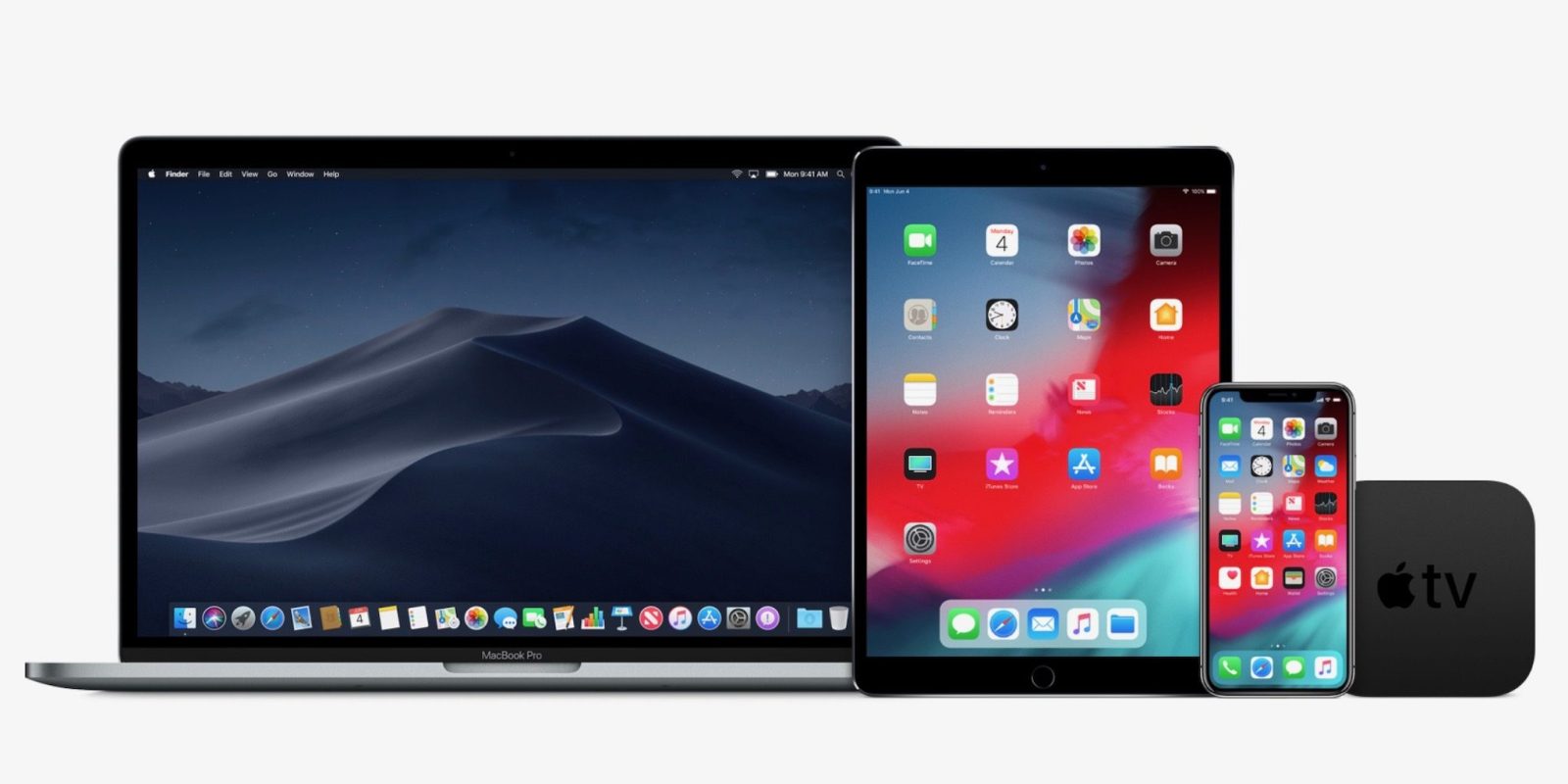
Role of the Workforce
The development of a highly skilled workforce can build deep understanding of how the production process works and allows workers at all levels to identify areas of the workflow to be improved.
- reduces costs
- empowers the workforce
- gives them a sense of ownership and loyalty to the company
Kaizen
Kaizen is a culture of continuous improvement originating in Japan and considered an important aspect of an organization's long-term strategy. It is a philosophy and commitment to continuous process and product improvement of processes in manufacturing, engineering, business management or any process.
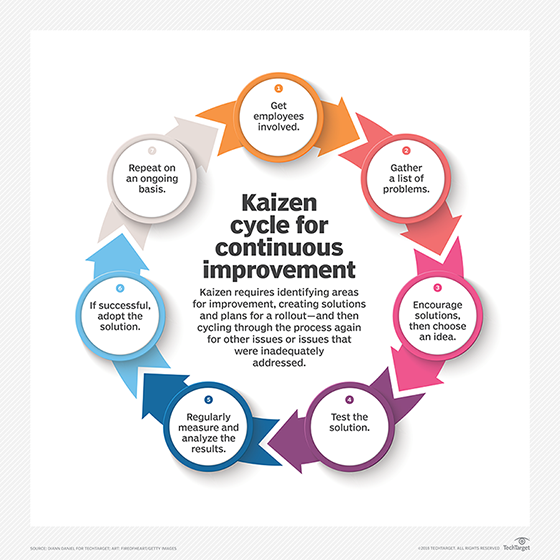
Toyota as a company embraces the ways of Kaizen in their manufacturing |
Lead time
Lead time refers to the time quoted to customers (usually in days or weeks) between the date of purchase and the date of delivery. (The time between the initiation and the execution of a process)
In industry, lead time reduction is an important part of lean manufacturing.

The 5 Ss: sorting, stabilizing, shining, standardizing, sustaining the practice
The Five S's are a formal approach to cleaning and organizing the workplace involving these five steps;
- Sort
- Set
- Shine
- Standardize
- Sustain
The 7 wastes: overproduction, waiting, transporting, inappropriate processing, unnecessary inventory and unnecessary/excess motion.
Of all these wastes, overproduction is the worst as it inherently incorporates all of the others. When you manufacture a product that will never be sold, the following happens;
- The raw material used is wasted
- The energy of the manufacturer is wasted
- The time and movement of the workers is wasted
- The transportation of the raw material and the finished product is wasted
Advantages and Disadvantages of Lean Production
Advantages
- Minimizes waste, reduces cost
- less impact on the environment
- Quickly adaptable to the market pushes
- Little capital is tied up in raw material or unsold stock
- Increased autonomy for workers - leading to higher moral
Disadvantages
- One problem in production stops the whole process
- Manufacturers rely on suppliers, one mistake by them halts production
- More suitable for large scale production
- When a certain level of refinement is met, using lean methods to squeeze more economy from production can discourage workers, reversing positive motivation and undermining your leadership
No comments:
Post a Comment